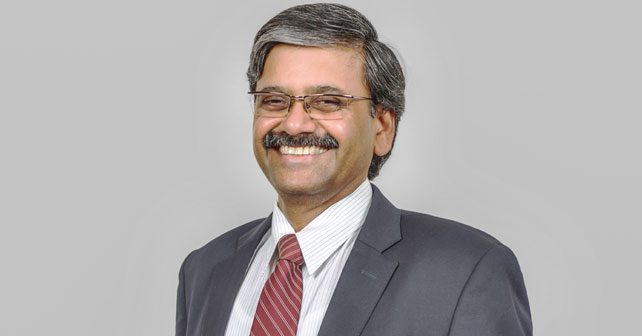
The Vitara Brezza is the first product developed from scratch by a team of engineers from Maruti-Suzuki in India. We talk to the man heading the development, Executive Director of Engineering, C V Raman, about the challenges his team faced.
The Vitara Brezza is generating quite a lot of interest, did you expect that?
Yes, we did expect the Brezza to generate a lot of interest. First of all, we’re quite proud of the effort, the responsibility given to our team, and then delivering what was expected of us – all the while following Suzuki global developmental processes. It’s been a great learning for the entire team, because the engineers that worked on the project made mistakes, learnt from them, and finally succeeded in delivering what was expected of them. And that’s the way to actually learn the practical aspects of vehicle development – there’s no better way to do it.
How long has the development process taken?
The discussion for this project started in April 2012 – June of that year we started working on it, and it took us three-and-a-half years to develop it. The first step was deciding what platform we wanted to use. We had the SX4 platform, and we had the brand new C-platform in Suzuki – and we had to decide which platform would be better in the long term, as well as in regards to weight savings too. The SX4 platform was an existing platform that would require lower investment, so it was a tough decision – but we took the decision to go with the new platform.
What was Suzuki’s involvement in that decision process?
They actually left the decision entirely to us, and told us to decide ourselves which platform we wanted to use. So, the new platform was capable of a sub-4 metre architecture, and the next challenge was how to make a layout to install the DDiS 200 engine. Our brief from the customer clinics, and research that we conducted, was very clear – it indicated that customers wanted ample boot space, with seating that’s flexible, and interiors that are smart. And the exterior design needed to be bold and masculine – so that way our brief was pretty clear. After knowing what platform and engine we were going to use, the first challenge was getting the proportions right as far as design was concerned, while also making sure the car was not too tall and had enough width so that three people could be seated in the rear seat. On top of that, we needed to have enough space for legroom in the rear and still have good boot space. It was very tough to get the design process passed by the top management – there were lots of rejections in the sketch stage itself, so that was a challenging process.
The involvement of the Japanese management, then, was only to the extent of what works and doesn’t work for the car?
No, they would just look at the model and make their suggestions about what they thought was right or could be improved – the final call of what to do was left entirely to us. The first decision was to sketch a 4-metre car with two design directions – bold, masculine SUV style or go for a crossover look. So, we went up to the clay model stage with both designs, but we finally decided to go for the bold, SUV look.
Regarding the testing and validation phase of the development, was that India based too – or was there contribution from the Japanese engineers?
We did the prototyping, all the stages of development, including the production engineering, tooling, weld shop, pressings, and even formability analysis here. There was some level of Suzuki help, yes, but most of it was done here by us. For validation of the vehicle, we did use the Rohtak facility for some parts of it – like for NVH and ride & handling. Endurance testing was done in the Gurgaon facility. But for cold weather testing, we had to use the facility in Japan – because we don’t have the facilities here. High-altitude testing, however, was done in the Khardung-La Pass area in Leh. In fact, even the crash testing was done in our Rohtak facility. But other tests, such as endurance, wind tunnel, rust, etc., was done using Suzuki’s facility – but it wasn’t done by the Japanese engineers, rather our engineers flew down to Japan and did the testing themselves.
The other exciting bit is the Boosterjet engine in the Baleno RS. What can we expect from it when you launch it later this year? And did you have to detune the engine for India?
The engine that we are currently showcasing is the European-spec version, with 170Nm of torque, but this is tuned for 95-octance European fuel and Euro-6 emission standards. For our Bharat IV fuel, which varies between 87 and 91-octance, we’ll have to retune the engine to accept both fuel qualities. There’ll be a marginal reduction in the engine output, but it’s still going to be a quick car. Other than that, we’ll add rear disc brakes in the Baleno RS, and will also make some small styling changes.
Also read: Interview with Saumitra Chaudhuri, ex-member of the Planning Commision
Write your Comment